News
News
- What is a sacrificial anode
- Basic requirements for reference...
- What does the reference electrode do...
- Why are zinc blocks attached to the ...
- What is the principle of impressed...
- What material does metal structure...
Contact
Phone:18739187123
hotline:0391-7588881
E-mail:970512272@qq.com
Address:Wuzhi County, Jiaozuo City, China
Company News
Use method of deep well anode
- Author:Libo
- Source:wm.voypictures.com
- Date:2021-08-15
- Click:0
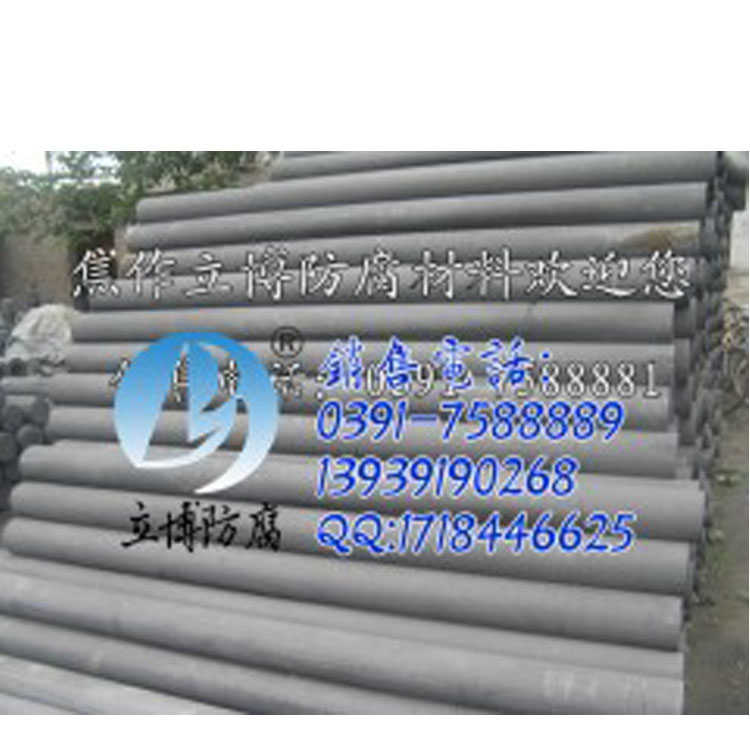
The deep well anode is vertical and the depth is less than 15m. It is mainly used as anode for cathodic protection system when surface space is narrow or surface soil resistivity is high. One of the advantages of using the deep well anode is that the distance between the anode and the structure to be protected makes the protection current distribution more uniform. In addition, the corrosion interference to other buried metal structures will be reduced. In order to facilitate the installation of anodes and ensure the engineering quality, the mixed metal oxide anode string developed in recent years has been widely used.
Construction instructions and requirements:
1. Anode well
(1) Anode well drilling machine: it can lift the object of two tons weight at least; Or drilling to match; At the same time, the normal operation of the drilling rig must be guaranteed.
(2) Derrick and well seat: must be kept perpendicular to the ground, not inclined, well seat must be firm, lifting anode body derrick raised height should not be less than 8 meters and vertical to the ground. At the same time, the carrying weight shall not be less than 2 stews. Caliper: First, 450mm drill pipe is used to drill 5m, and then steel casing (450*4*5000) for well protection is installed after the drill pipe is taken out. Then, 350mm drill pipe is used to drill to the depth required in the drawing. In addition, bentonite and yellow mud should be continuously added to cement the well in the process of drilling to prevent well collapse. Bell mouth or well shrinkage is strictly prohibited. After drilling the well, the well must be filled with water to maintain the well, in principle, not more than 1 hour; And check whether the well meets the requirements of the design.
2. Modular assembly of segmented prefabricated anodes
On-site welding of segmented prefabricated anodes ensures that the center line of anodes is vertically recombined. When hoisting and welding, the first group of anode lead wire from the second group of anode exhaust pipe through, at this time, one or two groups of anode body can be welded, welding, 273 splint must clamp the anode body, so as not to fall into the well; When the third group of anodes is welded, the first and second group of anodes leads are threaded out of the third group of anodes. Three anode leads are bundled together and ready to install the exhaust pipe; In the welding process, the welding must be tight, strong, must be welded twice, and no porosity, slag; The assembly and welding are carried out in the process of hoisting down the well. The welding personnel who weld the anode body must hold the welding grade certificate, and must ensure the normal operation of welding equipment and complete welding tools.
3. The assembled anode body is lifted into the well as a whole
The anode body must be hoisted in the central part of the anode well. After the hoisting group and assembly of the three groups of anode body are completed, the whole anode body is lowered into the well. One end of the 12 wire rope is used to pass through the lifting rings on both sides of the anode body and the steel wire is tightened. On the other end is connected to the winch started slowly down, below the 辺 edge to install the exhaust pipe, below the vent on the anode body at the same time open, install the exhaust pipe, plate lead by cable from the exhaust pipe, the anode lead not to cable outside the protection of the skin torn, also must exhaust pipe and the exhaust pipe on the anode body good and keep the vertical joint connection. When hoisting the anode body and installing the exhaust pipe, sufficient personnel, not less than 10 persons, must be employed.
4. Fill well with gravel
After the anode body is hoisted and installed in the well and the carbon filler is filled, gravel is filled into the deep well and the gravel is filled 0.5 meters down the well. When filling the well, keep the exhaust pipe in the center of the anode well. Be careful not to fill the exhaust pipe with gravel, so as not to block the exhaust pipe. Gravel must be compacted flat. The gravel size is 20mm-40mm.
5. Connection of anode lead cable and anode main cable
The three anode lead cables are connected to the terminal box and the post in turn. Ensure that the cables are firm and not loose. The anode main cable leads from the junction box. The anode main cable and the anode lead cable are connected with a 250*50*8 wiring copper bar. Four terminals (three lead wires and one main cable) are installed on the wiring copper bar. When the anode main cable passes through the anode main cable on the wellhead, the protective casing is added.
6. Build a well
Well platform foundation is 0.3m thick gravel layer, compacted. In the gravel layer with common red brick, cement masonry into cylindrical: outside diameter of 2.8m, inside diameter of 1.2m. At 0.15m from the ground, the wellhead is built into a square column with 1.5m in length and width, 0.65m in height and 0.7m in diameter. The anode main cable hole, aperture 80mm, is reserved when laying the well platform. The inner wall of the well platform is smoothed with cement, and the thickness is 10mm. The total height of well platform foundation and well platform is 1.6m, the shape of well platform inner cavity is pear-shaped, and the well platform is 0.5m above the ground. The cement is 20#, the brick is ordinary red brick, and the gravel size is 20-40mm.
7, deep well anode installation well seat, well cover
Customize well seat and well cover in the factory according to the size and process requirements in "anode well seat and well cover structure drawing". Place the well seat on the well platform. The center of the well seat is aligned with the center of the wellhead. The well seat is reinforced with bricks and cement slurry so that it is connected with the well platform. The center of the well seat is aligned with the center of the wellhead. The well seat is reinforced with bricks and cement slurry so that it is connected with the well platform. Also use the plank to maintain to cure, dry. The well seat and well cover are made of gray cast iron HT15-32 and added with asphalt for anticorrosive. The cement is 20#.